Von Anfang an dabei
C 400 U | Emde | Tool making
Swen Emde illustrates how to turn a lack of job prospects and trust in the following generation into a successful mould and tool making company. After the company was founded in 2016, he immediately invested in a 5-axis machining centre from Hermle with the assurance that he would be able to machine tools and machine parts on it precisely and efficiently without risking downtimes.
Swen Emde is a skilled tool mechanic. After his career outlook in his original training workplace was lacking, he entered the business his father had run for 26 years. Wilfried Emde had been producing single-variety granulate from plastic waste at the Diemelsee Recycling Yard for 23 years. After Swen Emde had passed the examination for Master Precision Mechanic, he developed the idea of expanding the family business to include toolmaking and mould making.
In addition to three CAD/CAM workstations, he built a machine park including a wire eroding and turning machine as well as two machining centre from Maschinenfabrik Berthold Hermle AG. "We were already impressed with the reliability of Hermle machines from our previous employer", confides the Managing Director. "If you have only one machine, as we did in the beginning, you have to be able to rely on it 100%", emphasises Benjamin Finck. He is a project manager and about three years ago Swen Emde talked him into setting up the toolmaking area with him. Its highlight is the C 400 U 5-axis system that Emde uses to produce not only the moulding dies for the plastics industry, but also prototypes for furniture and automobile manufacturing. One year later he invested in a C 400 V. He uses the 3-axis machining centre mainly to prepare the workpieces quickly and effectively for precision machining on the 5-axis machine.
-
Thanks to its precision, the C 400 U achieved the repeat accuracy required by Emde.
In use around the clock
The milling centres are programmed exclusively by computer using HSM Works or SolidCAM. The subsequent machining time for individual workpieces are between two and 80 hours. This means: While toolmaking is a purely one-shift operation with five employees, the 5-axis machining centre runs into the night. That increases the productivity of the small company considerably. "Of course that means trusting the machine to be able to work in unsupervised shifts as well", stresses Emde.
"OF COURSE THAT MEANS TRUSTING THE MACHINE TO BE ABLE TO WORK IN UNSUPERVISED SHIFTS AS WELL"
Hermle was also a decisive contact point when a specific manufacturing problem came up: "We were faced with the challenge in a small series of having to produce a turned surface inside the component", recalls Finck. Their consultant finally led them to interpolation turning. "By upgrading the control with an additional program, we were able to produce the rotation-symmetrical contours in the required surface quality with a milling tool", adds the project manager. This option is an absolute win for Emde: "We are one of the few companies in the North Hesse district that is able to offer interpolation turning", notes Swen Emde.
"Everything is working just as we imagined it", summarises Swen Emde. Considering the high level of utilisation, however, there is one thing he would do differently: "Seen from the perspective of today, we would also invest in an automation solution."
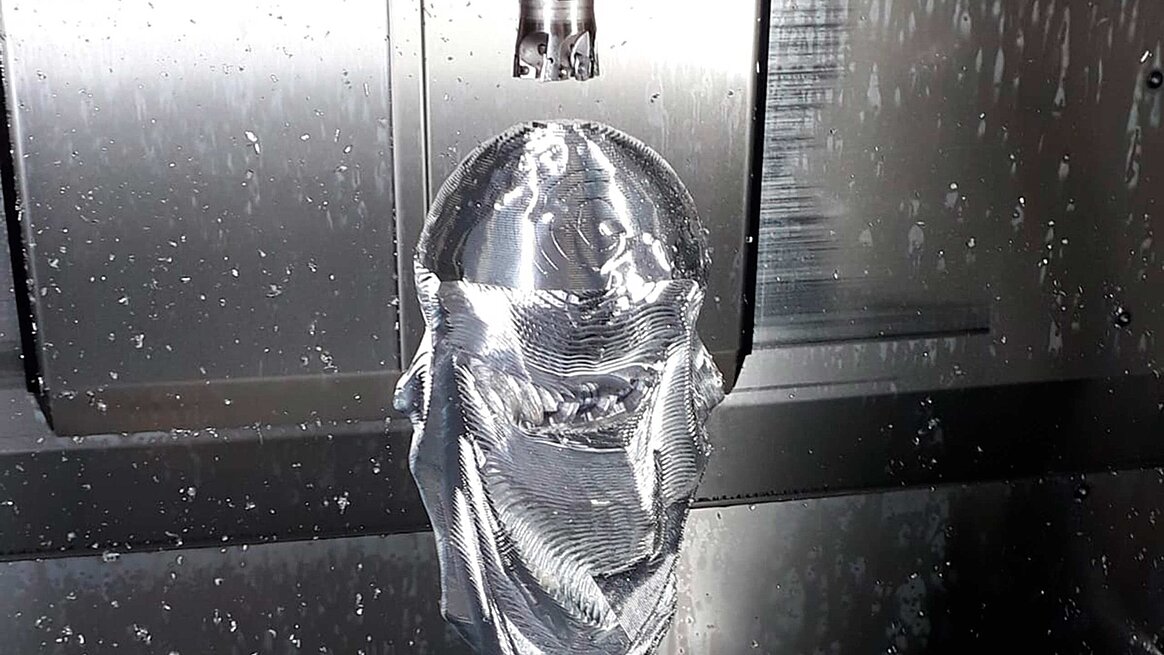