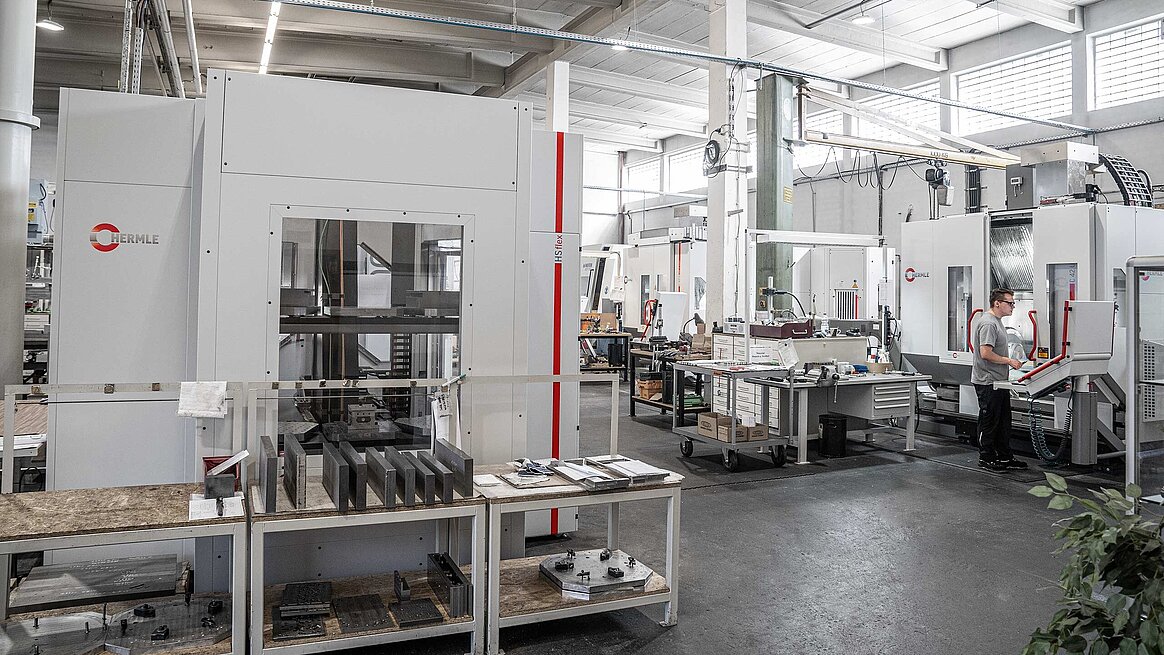
Concept of rotational machining alone has had its day
Although the addition of an automation solution represented remarkable growth, there is still more to the story. When Matthias Reh wanted to replace an old turning machine that dated back to the company's founding, he contacted Hermle directly. "Often our turned parts still had to go on the milling machines because there was still a bore hole to drill or a groove missing. That made it clear to us that we needed a machine that could do both, he explains. So he focussed on the machining centres of the High Performance Line with Mill-Turn functionality (MT). There was very little time between the initial contact and the sales contract: At the beginning of 2019 he received an offer to purchase a demonstration machine type C 42 U MT after the in-house exhibition two weeks later. "We settled financing issues with the bank, had another up-close examination of the milling-turning centre at the in-house exhibition in Gosheim and signed the contract. It went so quickly that we had no time to think about possible alternatives," remembers Matthias Reh. He never regretted it.
With the new manufacturing capabilities came new customer in medical technology and the energy sector. The challenge this brings with it is the diversity of materials. For example, Reh and his team machine both cast steel and titanium on the C 42 U MT. The shapes of the valves and other features are often similar or even identical. Only the material is adapted for the intended purpose. The geometries are less problematic: "There is actually nothing complex on the Hermle machine if you have the right machining strategy in mind," notes the industrial mechanic.
But it is not quite as simple as that. "In the beginning I underestimated the technology. For example, it is very important how the component is clamped. Otherwise dangerous imbalances will develop during rotational machining." Reh cites this as the cause of an extra two or three weeks in the introduction phase compared to simple milling centres . "Now it runs just as reliably and stably as the other machines."
Although the milling/turning centre has only been in use at Der Span since September 2019, the investment has paid off for the young company. "The fact that we are manufacturing on Hermle machines often eliminates the question of whether we are up to accepting an order in terms of quality," reports Reh, who seems almost a little surprised that Hermle is a solid selling point.
The three machines from Gosheim are all working at full capacity. Of course productivity has risen, although this must be understood in a nuanced context: "We started with antique systems," says Reh, putting matters in perspective while drawing an overall positive conclusion: "I have never regretted buying Hermle machines. Along with the quality and precision, we were impressed from the very beginning by the Service Department, which had a solution on hand for every problem." It hasn't even been two years yet – who knows where this will lead in the future? "Of course we are aiming for further growth. When the next investment will come is not clear yet at the moment. But there is no question that it will come," promises Matthias Reh.