For efficient production.
Workpieces of various shapes, sizes and weights can be handled automatically by handling systems to save costs and time.
Overview of handling systems
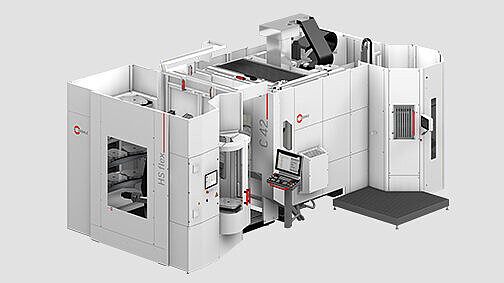
Handling system HS flex
Available for the HERMLE machining centres C 250, C 400, C 12, C 22, C 32 and C 42
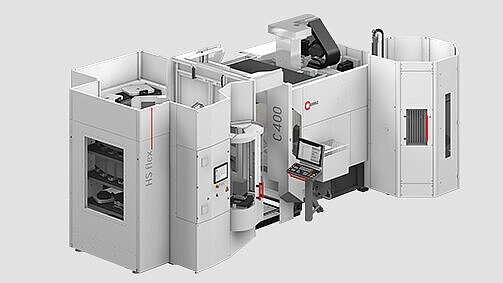
Handling system HS flex hybrid
Available for the HERMLE machining centres C 12, C 22, C 32, C 42, C 250 and C 400
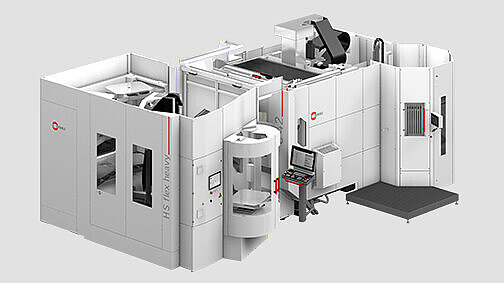
HS flex heavy handling system
Available for the HERMLE machining centres C 400, C 650, C 32 and C 42
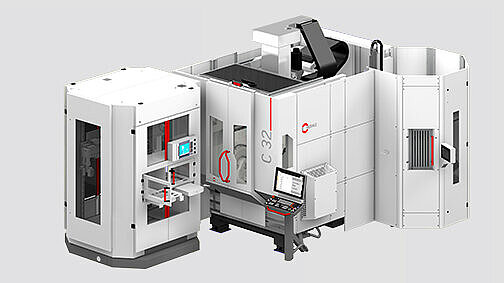
IH systems
Available for the HERMLE machining centres C 12, C 22, C 32 and C 42
User reports
Discover what our customers say about us.
Update only with automation
Cafmeyer
Tool & mold making
Cafmeyer manufactures press moulds. The more complex the part, the more parts needed for the mould. In the past, the Belgian mould maker was sometimes pushed to the limits of its capabilities – both in terms of dimension and capacity. The company therefore decided to invest in a Hermle C 650 U 5-axis machining centre with HS flex heavy automation.
Ensuring efficiency and high-end quality
Dieter Wiegelmann GmbH
Plastic engineering
Injection molding
Wiegelmann is an expert in aluminium and steel mould making and plastic injection moulding. The mould maker is a stickler for deadlines and perfection, even when the parts have complex geometries. When it comes to machining, Wiegelmann relies on Hermle. HS flex automation arrived at the German company in the shape of the new C 42 U, making sure its range of machinery is even more flexible and versatile.
Know-how in both directions
Jung Werkzeugbau GmbH
Tool and mold making
Jung Werkzeugbau GmbH is expanding its mechanical production capacity: an automated C 42 U from Hermle is set to expand the company’s three-shift operation to include unmanned night-time and weekend shifts. Those responsible for paving the way are overcoming the last optimization hurdles and installing additional safety features.
- The handling systems
More productive manufacturing: Handling systems facilitate significant time and cost savings. The automated handling of workpieces of various shapes, sizes and weights minimises the time required for ancillary activities by 35% on average. This leads to an enormous increase in productivity.
Every production operator knows: The more automation, the less monotonous and sometimes physically demanding the tasks for workers. The energy-sapping effort often yields little to no reward – in fact, it can have quite the opposite effect. Manual setup and tool changing by production staff inevitably limits the cost efficiency of the machines. In the production environment, a robust automation solution proves significantly more effective, as the performance spectrum of a handling system surpasses the capabilities of the human body by a considerable margin. With that said, it is not only legitimate, but also in line with the times, to let handling systems do the majority of the tasks. For the benefit of staff. And for the benefit of productivity. In times of staff shortages, regular operations can be sustained and night shifts made available to fit in with work schedules. All this equates to more increased flexibility – benefiting the operator directly and the entire company indirectly.
If you choose a HERMLE handling system, we guarantee uncomplicated and rapid commissioning. After delivery, the compact system is quickly set up and ready for operation, requiring no floor anchorage during installation. Rethink handling – with the handling systems from HERMLE, a leading manufacturer of CNC milling machines and other precision machines.
- What is handling technology?
Handling systems utilise handling technology, a dedicated automation technology tailored for machining centres in machine production. Its use can considerably reduce non-productive periods and save an enormous amount of money, as not only the machine-hour rate but also staff costs are minimised significantly. This helps to optimise time management as a whole: You can strategically deploy staff to areas where their skills are needed most. These structural changes will ultimately enhance the manufacturing efficiency of your company. Handling systems operate on the principle of automation, facilitating the rapid transport of workpieces and products to a connected machining centre, while also enabling easier (temporary) storage. The production cycle is, therefore, optimised by simplifying the handling of components with diverse properties – hence the apt name for the system.
What does this mean in practice? Integrating a handling system into your machining centre enables the simultaneous execution of various processes, allowing for parallel setup and adjustment, for example. Consequently, downtime is minimised throughout the entire intralogistics process. Essentially: Reduced order throughput times, greater production capacities and lower hourly rates, thus marking a breakthrough on several levels.
- How are HERMLE handling systems designed?
A handling system is a versatile and configurable complex directly linked to a machining centre. The front-sided adaptation has the advantage that the direct connection to the production machine ensures a particularly space-saving layout. Each HERMLE handling system consists of several basic components: In addition to the core of the handling system, which includes the 4-axis unit comprising precision components, along with one to a maximum of two storage modules boasting ample storage space and adequate pallet pockets, the setup station is another critical component of a handling system. The setup station is designed to support heavy weights, offers optional rotation capabilities and can be ergonomically loaded using a crane. An extensive intermediate space provides the operator with direct access to the working area to perform manual activities there. Gone are the days of laborious pencil work and back-breaking tasks, whether during setup, order entry or program adjustments. Everything within easy reach.
A swing door locks access to the working area in automatic mode. In setup mode, however, access to the handling system is locked. This guarantees complete safety for the operator and protects the machine from foreign objects in automatic mode. An external control centre is installed for manual setup and control of the automation solution: The touch panel can be operated intuitively thanks to the HACS (HERMLE “Automation-Control-System”) software by HERMLE – this technology facilitates intelligent order processing and boasts an exceptionally user-friendly display. Even staff trained at short notice are guided step by step through the setup, operation and daily maintenance tasks for the handling system.
The software offers a number of features: In addition to calculating the runtime in advance, HACS also indicates scheduled tool usage. The operator can define the quantity of components for the order and prioritise and schedule the order accordingly. Preliminary planning can be dynamically adjusted throughout the entire duration of the order. Our in-house developed HACS system is control independent and compatible with Siemens and Heidenhain machines, providing complete flexibility in this regard as well.
The system’s integrated bar code scanner swiftly captures new orders within seconds, enabling efficient order checking and processing on the panel. There is no faster or simpler way to launch new production projects.The aforesaid core of the handling system comprises a 4-axis unit with a manipulator, designed with a sturdy feed axis in the gripper. The highly sensitive gripper technology effortlessly initiates movement and positions even the heaviest workpieces into empty pallet pockets, facilitating precise and intelligent positioning of various components, including oversized ones, without any difficulty.
- How is handling equipment deployed?
Not all handling equipment is the same: Depending on the actual production project and product range, universal (HS flex handling system) or more powerful automation solutions (HS flex heavy handling system) are available from HERMLE. Loads weighing up to 1200 kg can be transported by our most powerful handling system, for example. On request, we will be more than happy to advise you on which handling system best suits your machinery and the individual conditions in your production facility. Simply use our service whenever you need to.
- Productivity meets ergonomics.
The primary objective in developing the HS flex family is to optimise productivity. Additionally, we have meticulously rethought ergonomic aspects to ensure that operators and service staff can work swiftly and without fatigue in every work scenario. No long distances – you can take our word for it. HERMLE handling systems are designed to provide operators with all three access points conveniently located on the same side for setting up the order, positioning parts within the working area and controlling the control panel.
- What else characterises HERMLE handling systems?
HERMLE is said to hold the leading position in cutting-edge mechanical engineering. This also applies in particular to our handling systems. Thanks to their robust design, our premium solutions boast exceptional durability, representing investments for the long term. Our handling devices prioritise the highest quality within a minimal footprint, meticulously crafted by HERMLE engineers to be as space saving and compact as possible. Their remarkable ease of use stands out – with the intuitively designed touch panel, having to go through complex operations no longer requires navigating through a confusing array of buttons. Thanks to an easy-to-understand software program, the user interface is intuitive and guides you through various options with clear, straightforward instructions. This allows you to create and manage orders in next to no time. New orders can be added using a bar code scanner. The tedious task of entering and correcting long numerical codes is now a thing of the past, forever.
An additional benefit is the customised configuration of the memory modules. This stems from the fact that shelves can be adapted to accommodate the largest workpiece dimensions of an order. The option to significantly increase the storage capacity with a second storage unit opens up new avenues for production potential. Up to 50 pallets can be stored. The automation solution can be perfectly tailored to the setup of the rack storage system, ensuring efficient utilisation of every square centimetre within the rack storage.
And you are also flexible when it comes to combining the handling system and the HERMLE machine. As part of an individual, no-obligation consultation, we will find out which handling system is best suited to your production situation and how the productivity of your company can be optimised. With the help of our competent team, you can determine your success model.
- Planning, monitoring, controlling.
HACS technology ensures you have all relevant information to hand: Intuitive operation in the categories system overview, work plans, pallets, tasks, tools, sequence plan and operator tasks. The software enables control of the automation with easy-to-understand, graphically and intuitively structured operating patterns, for example easy pallet transport via drag-and-drop. The tool analysis saves time and makes things easier for recently trained staff: The program informs the operator which tools are not required and when the last and next use of the tool component is planned. Manual tasks assigned to the operator on the panel are clearly depicted and managed, ensuring uninterrupted processing and significantly minimising organisational downtime. Thanks to the compatible HACS Connect application, you can monitor and update handling system settings in real time at any time.
- Handling systems are not pallet changers.
HERMLE gets things moving. And that includes every type of pallet. Unlike conventional pallet changers, the handling systems shown here offer far greater flexibility in many aspects. Firstly, handling systems are compatible with a wide array of formats and pallet sizes. Secondly, their basic system can be docked quickly onto almost any HERMLE machine and be supplemented with additional modules as required. While handling systems and pallet changers share the common feature of uncompromising docking, pallet changers are restricted to a standardised pallet dimension.
The handling systems are also more flexible in another respect, too: They can be variably adapted to the parts spectrum of a machine. Since HERMLE handling systems are true to the motto: High mix, low volume. Many HERMLE customers do not know today which parts will be manufactured tomorrow. But that is definitely not a problem with the HERMLE modular solutions. Thanks to a large range of pallets, collision contours can be optimised, something that is not so easy with a conventional pallet changer. Overall, you achieve a low initial investment and an optimised long-term footprint – resulting in more pallets per square metre within the system.
HACS makes automation easy: A dashboard facilitates adapting work plans and managing tools for use. In combination with HIMS, everything can also be controlled remotely from a desk or mobile tablet. In both variants, process data can be retrieved instantly thanks to state-of-the-art NC programs. To process an order, the intelligent software automatically checks whether the zero points are loaded, the pallet is in the system and the machine has been set up with the respective workpiece. And, of course, whether all the tools are available in the system to process the specific order. In the event of an error message, maintenance or downtime, the operator is informed immediately via real-time transmission.
All the relevant information is stored on the server and can be accessed locally at any time. This guarantees that staff always have an overview of downtime procedures and tool requirements. Other machines are also informed of the exact process sequence and all the work steps, as HERMLE handling systems also transmit their data to neighbouring networked machines. An innovation that makes IoT –the Internet of Things – possible. This type of networking optimises the entire process chain, now and in the future. Automation offers you significantly higher production capacities and allows you to remain competitive thanks to the fully automated process. Today, progressiveness is at the heart of any corporate philosophy. The various models of HERMLE handling systems offer an excellent choice for both the manufacturing and packaging industries, catering to companies of varying sizes, requirements and capacities. They provide a means to organise production flexibly, securely and economically for the future. We are always more than happy to inform our customers and partners about future automation solutions and new products