Industry 4.0 and the Smart Factory
The digital transformation is now becoming the focus of many different production operations. HERMLE is there to provide support while you chart your individual course towards Industry 4.0 and the smart factory. We offer a wide range of software solutions for improving your efficiency, precision and productivity. Our digital modules thus represent links in the chain of smarter production. We can work together in order to find out what your operation needs. With Digital Production, Digital Operation and Digital Service modules, we can put together a comprehensive package that will put your HERMLE machining centres on a firm footing for future tasks: Intelligent order management and transparent machining processes, smart machine tuning, paperless manufacturing and sophisticated technology cycles, as well as options for remote or preventive maintenance. Our digital modules improve productivity, ease of operation and efficiency.
HERMLE Digital Production
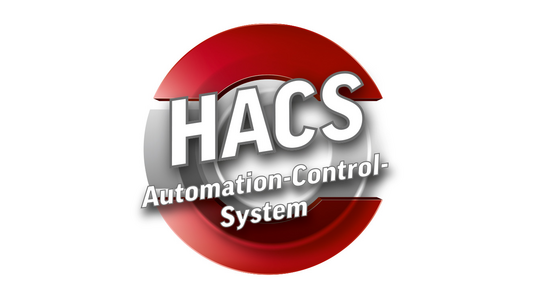
HACS – intelligent order management
- Forecast of runtime and tool usage
- Intuitive assignment of NC programs and zero points
- Order definition for piece counting, order prioritisation and planning
- Dynamic sequence plan modification
- Control independent and can thus be used for Siemens and Heidenhain
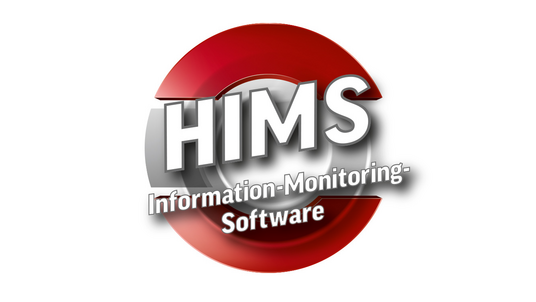
HIMS – the central monitoring tool
- Compact overview of the machine(s) with Live Status
- Detailed evaluation of the status history
- Display of the message history
- Export function for status data to .csv-format
- Order preview (only in combination with HACS)
- 24h email notification of incidents or faults affecting the machines
- Calendar function to define the notification periods
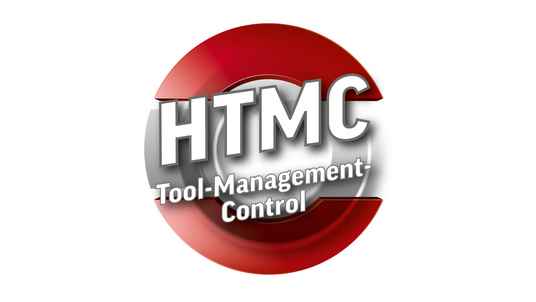
HTMC – convenient tool management
- HERMLE’s own supplement for extended tool management for Heidenhain controls
- Assistance for organizing tools and optimizing setting up tasks
- Optimised magazine assignment by means of tool geometry computation in the pick-up tool magazine
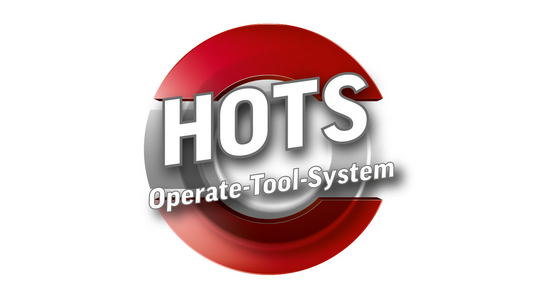
HOTS – convenient tool management
- HERMLE’s own supplement for extended tool management for Siemens controls
- Assistance for organizing tools and optimizing setting up tasks
- Optimised magazine assignment by means of tool geometry computation in the pick-up tool magazine
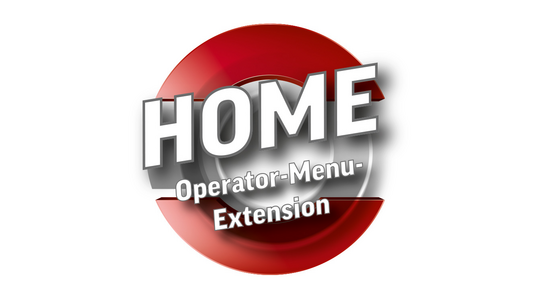
HOME - customisable views
- Overview of essential information on the HOME screen
- Control independent
- Interface can be defined individually to match operator’s specific requirements
- With HACS, current order information
- With HIMS, data of networked machines
HERMLE Digital Operation
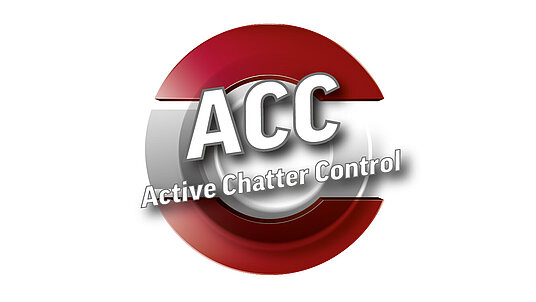
ACC - Active Chatter Control
During power cutting, the strong process forces acting through the milling tool generate vibrations in the machine structure. If certain limits are exceeded, this can lead to tool damage, workpiece damage and/or machine damage. ACC computes a compensation signal from the number of cutters and the rotational speed of the spindle, resulting in reduced vibrations. This means that higher rates of feed, input and tool usage times are possible, making for more productivity and lower costs.
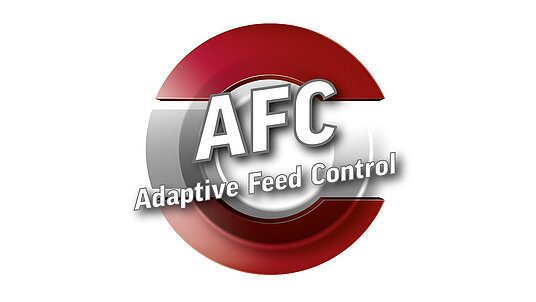
AFC - Adaptive Feed Control
Depending on the maximum amount of input to be expected, you can define maximum process parameters and limits using AFC. If the actual input is lower on account of varying cutting depths in the component, AFC increases and permanently monitors the tool-specific process limits based on spindle performance and feed rate. In this way, the software increases process reliability and productivity.
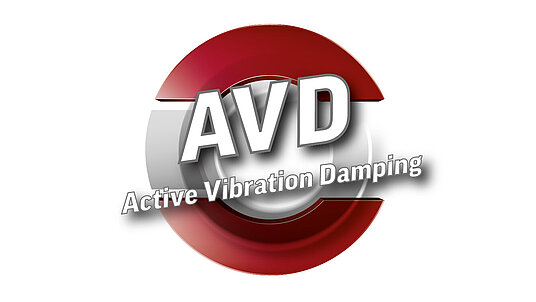
AVD - Active Vibration Damping
Machine tools are elastic systems. Vibrations caused by abrupt acceleration lead to varying degrees of precision at the tool centre point. These axis vibrations are compensated by the continuously active AVD software, resulting in improved surface quality, precision, feed rates and productivity.
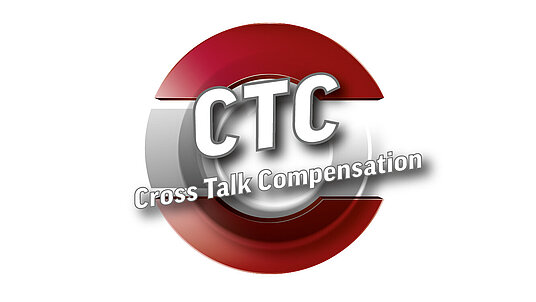
CTC - Cross Talk Compensation
The effects of mass inertia and structural flexibility mean that acceleration of the axes can lead to displacement of the tool centre point. Which in turn produces inaccuracies in machining. The permanently active CTC feature compensates for these acceleration-dependent displacements at all times. This improves contour accuracy, precision, feed rates and productivity.
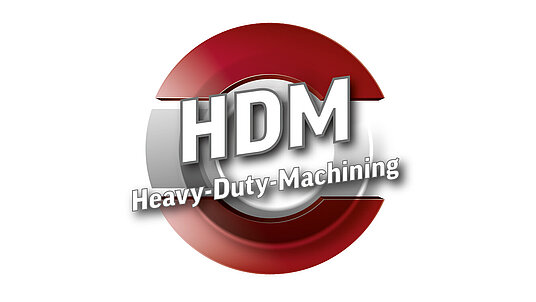
HDM – Heavy-Duty Machining
- For roughing in conjunction with high milling power
- Greater machining performance possible on account of reduced machine vibrations (depending on the tool and the selected technology data)
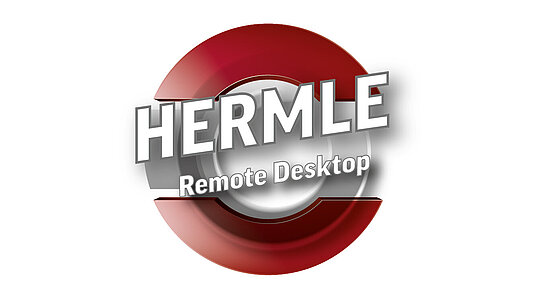
HERMLE Remote Desktop
- paperless manufacturing
- direct connection to your IT infrastructure
- Use of your familiar in-house applications
- All the information you have on your PC directly available at the machine
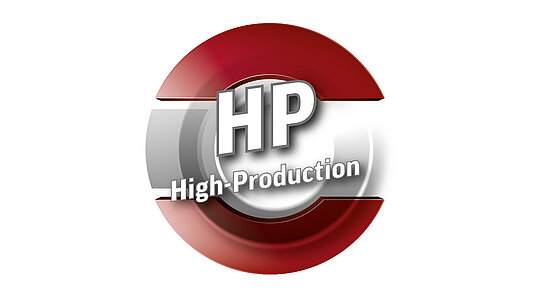
HP - High Production
Used for quicker machining with programs which have many cycle calls or subprograms.
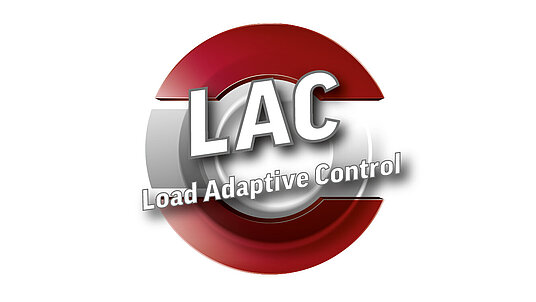
LAC - Load Adaptive Control
As standard, the drive parameters for machine tools are set to cope with the maximum expected workpiece weight. LAC adapts the settings for the rotary axis according to the workpiece. This means you benefit from maximum dynamic capability for each workpiece. Accordingly, HERMLE machining centres with swivelling rotary tables achieve better precision, surface quality and acceleration.
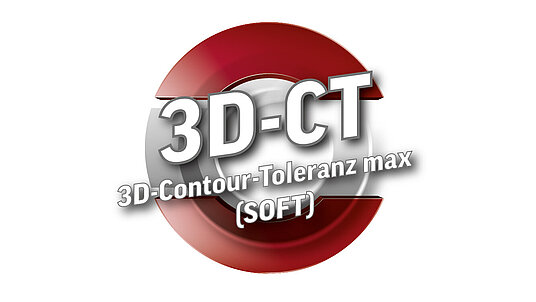
3D-CT - 3D contour tolerance max. (SOFT)
- For 3D roughing with low machining performance
- Very high machining speed, mainly for free-form surfaces
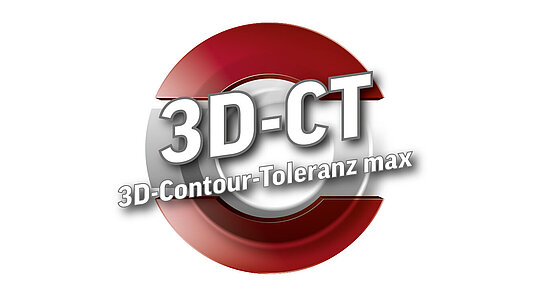
3D-CT - 3D contour tolerance max.
- For 3D roughing with low machining performance
- Very high machining speed, mainly for free-form surfaces
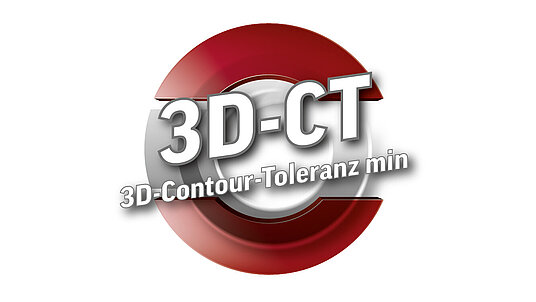
3D-CT - 3D contour tolerance min.
- For very high machining quality demands, mainly for free-form surfaces.
- Can also be used with conventional programs.
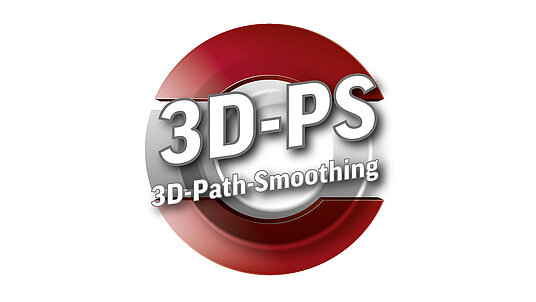
3D-PS - 3D contour smoothing
For very high demands on the surface quality, mainly for free-form surfaces.
HERMLE Digital Service
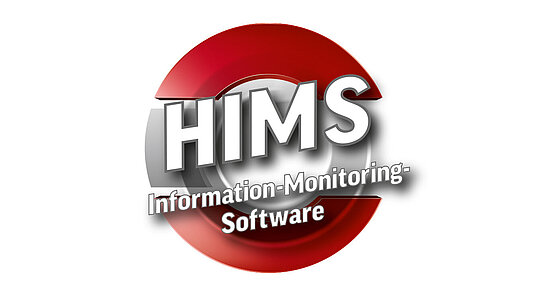
HIMS – the central monitoring tool
- Compact overview of the machine(s) with Live Status
- Detailed evaluation of the status history
- Display of the message history
- Export function for status data to .csv-format
- Order preview (only in combination with HACS)
- 24h email notification of incidents or faults affecting the machines
- Calendar function to define the notification periods
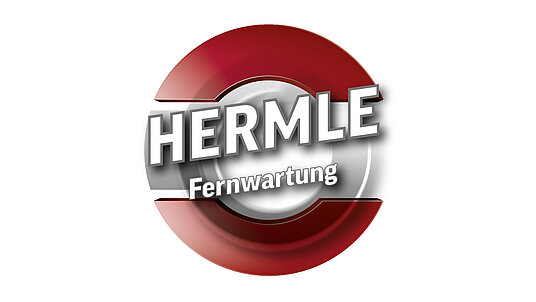
Remote maintenance
- Fast help from qualified service technicians
- Avoidance of service calls
- Fast identification of causes
- Support for operation / programming directly on the customer’s machine
- The customer can terminate a session at any time
- Independent of control system variant
- Secure connection to HERMLE
- Simplified data transfer for updates/service files/ ...
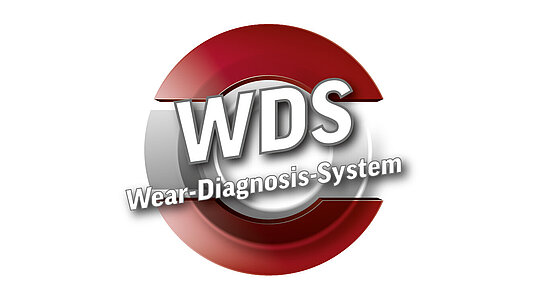
WDS – maintenance diagnostic system
- Analysis of running behaviour of the linear and rotary axes
- Determination of the frequency spectra of the linear and rotary axes
- Evaluation of all relevant sensor data
- Determination of vibration values for the tool spindle
- Determination of the machine accuracy
- Determination of temperatures of drive motors
- and tool spindles
- Data analysis and diagnosis by qualified
- HERMLE technicians
- Regular protective earth conductor check